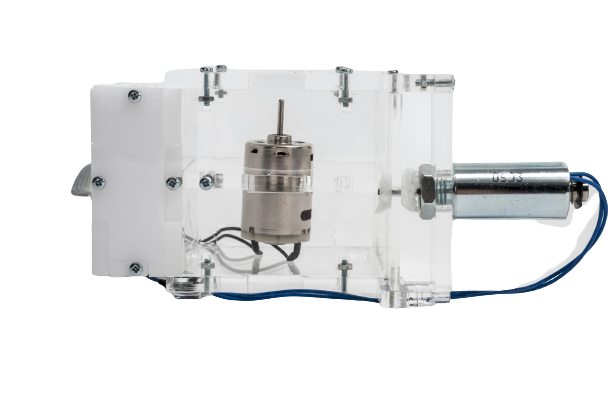
MUTOR
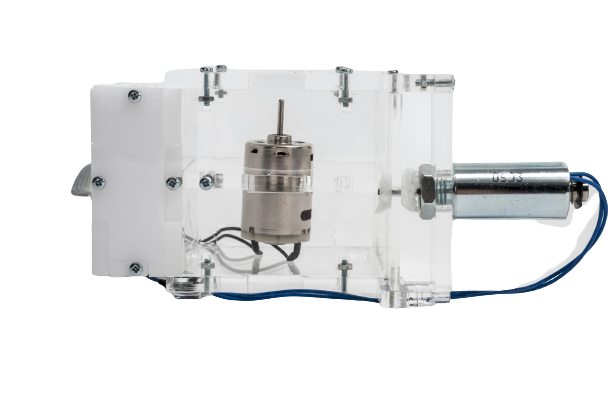
The instrument is designed in two different models: horizontal (H-model) and vertical (V-model). Both models are comprised of a thin sheet of steel, a strip of bright LEDs, which is placed in an open-faced square tube made of white acrylic, and push solenoids (2 in H-model and 1 in V-model), which are all held together in a transparent acrylic frame. Aside from the orientation of the steel sheet and the frame and the number of solenoids, the two models slightly vary in terms of the direction of actuation, as well as the thickness of the sheet. In both models, microcontroller programming is used to drive the solenoids and put the steel sheet into motion and vibration. The frequency and amplitude of the actuation is controlled using MIDI messages. In addition, in both models, each solenoid has a corresponding strip of LEDs whose luminosity is associated with the amplitude of the actuation. The use of mechatronic and microcontroller programming makes it possible to use Rippler in both interactive live performance and self-governing installation settings.
Mo Zareei
Mentors: Ajay Kapur , Dale Carnegie
2015
Bridget Johnson
The instrument is comprised of a DC motor, a push solenoid, a 3D-printed plastic disk, a piece of sharp-edged spring steel, and an LED strip. These components are all held together in an open-faced enclosure made of clear acrylic. The noise is generated when the spring steel makes contact with the spinning 3D-printed disk that is attached to the DC motor: as the solenoid pushes out and the sharp tip of the bent spring steel touches the spinning disk, it vibrates rapidly and generates a high frequency rasping sound. A 12V push solenoid is used to switch the contact between the spring steel and the spinning disk on and off. Therefore, system’s rhythmic behavior – simple or sophisticated patterns, pulses, and pauses – is determined by solenoid movements. The amount of force applied by the solenoid is the main factor in determining the amplitude of each event, and modulation in the speed of rotation creates a timbral range and introduces a subtle and relative sense of variety to the pitch domain. The disk’s revolutions are actuated by the rotary motion of the motor shaft, and the LED strip lights up the entire unit once there is an event (a contact between the spring steel and the disk). The luminosity of the LED strip corresponds to the loudness of each event. The solenoid, the motor, and the LED strip are all controlled via a microcontroller (an Arduino board), driven by a custom-designed PCB board that functions as an Arduino shield.
Mo Zareei
Mentors: Ajay Kapur , Dale Carnegie
2014
The Novalis consists of a power supply, microcontroller, two actuator driver boards, and accompanying input and output interfaces. The 500 watt power supply was chosen as its output voltage matches the majority of solenoid actuators used by the authors’ projects; the power supply’s current rating could handle switching potentially large number of actuators connected to the Novalis interface. As a meta-module whose role is to easily connect actuator modules with a host device, the means by which the Novalis interfaces with host devices and actuators is important. To interface with host devices, a USB cable is used; actuators are connected via 5 mm barrel-type jacks which are wired to the Persephone boards. While Novalis may be used with any compatible actuators, two new systems were developed to utilize its rapid deployability and ease of use.
Ajay Kapur, Jim Murphy, Ness Morris, Bruce Lott
2013
MalletOTon does not require the original instrument to be modified in a permanent or damaging manner. This allows MalletOTon to be easily removed from its current instrument and attached to another marimba or metallophone. The actuators are mounted on brackets to a length of T-profile aluminum extrusion, allowing for easy repositioning of the actuator modules. MalletOTon uses 48 rotary solenoid actuators. Such rotary solenoid actuators are the simplest type of robotic percussion end effector, and were chosen due to their ease of implementation. Attached to the shaft of the solenoid is a rubber-tipped mallet. Upon application of voltage to the solenoid, the mallet rotates into contact with the marimba’s bar.
Michael Darling, Eric Heep, Ajay Kapur
2013
Lydia is a project mentored by Trimpin to modify an existing piano into a system for new composition. There are a series of spinning bow wheel motors that activate individual strings. There is also a set of push solenoids that activate sets of strings. There is also a saw installed at the bottom of Lydia that makes scraping sounds.
Eric Heep, Jason Jahnke, Daniel Reyes, Ajay Kapur
Mentors: Trimpin
2013
Each Modulet consists of a clapper-style solenoid actuator attached to a length of aluminum extrusion. The hollow square-profile tubing serves two purposes. Firstly, it functions as a resonator for the module’s solenoid actuator. In this role, it amplifies the solenoid’s clapping sound produced upon actuation. Secondly, the extrusion serves as an attachment point for a hanging assembly, allowing the Modulet to be equipped with a wire braid hanger. With this hanger, each modulet may be attached to wire trusses or other mounting systems common in gallery spaces.
Ajay Kapur
2013
Kritaanjli is a robotic harmonium with 44 solenoid actuators and a variable-speed bellows pumping mechanism..
Kritaanjli consists of an aluminum framework which surrounds a harmonium. Attached to the framework assembly are three major subassemblies: the electronics enclosure, the bellows-pumping mechanism, and the keyboard actuation mechanism. T-bracket aluminum extrusions were chosen as the materials for Kritaanjli’s framework due to the flexible modularity which they afford: mounting subassemblies to the aluminum extrusions proved simple and efficient. The electronics enclosure houses the microcontroller and daughterboards and is mounted directly on the frame to minimize distance of cable runs. To pump the harmonium’s bellows, a DC electric motor is connected by means of a crank mechanism first to a crankshaft and then with a clamp directly to the rear of the bellows. The crank travels about the motor’s hub on a wheel with a diameter equal to the harmonium bellow displacement. To vary the harmonium’s output volume, the motor speed can be increased; additionally, harmonium motor speed must be increased to maintain a constant volume as more keys are depressed. Key presses are achieved through the use of linear DC solenoids arranged in an array above the harmonium’s keyboard. Each key has an accompanying dedicated solenoid. The solenoids are mounted on an aluminum bracket and are connected individually to a MOSFET driver board contained within the electronics enclosure.
Ajay Kapur & Jim Murphy
2012
Glockenbot is an electro-mechanical metallophone with timbres similar to a glockenspiel. The bot utilizes 13 CalTron solenoid beater assemblies which were designed at CalArts for this instrument, emphasizing a low-cost approach to fabrication. The CalTrons strike hand-tuned 6061 T6 aluminum bars – an aluminum alloy with particularly resonant properties. The instrument can play a chromatic octave from D4 to D5 and was designed without a damping system to permit tone clusters with very long decay times. Built in the spring of 2010, Glockenbot premiered during the CalArts Machine Orchestra show on May 13th, 2010. In February 2011, the bot was completely revamped with faster beater assemblies and new electronics & wiring. Additionally, two actuated slinkies were mounted to the frame for amplified laser-like sounds, because it was determined that the Machine Orchestra needed to incorporate more sci-fi laser-like sounds. Built on the base of a discarded office chair, Glockenbot is controlled via HIDUINO, a custom MIDI firmware for AVR microcontrollers.
Dimitri Diakopoulos, Michael Darling, Ajay Kapur
2010